La manutention des poudres en environnement agro-industriel met en œuvre de nombreuses normes et directives. Certaines visent à garantir la sécurité alimentaire et la santé des consommateurs. D’autres protègent la sécurité des personnes présentes sur le site industriel ou à proximité. Les directives européennes ATEX fixent les conditions de conception et d’utilisation des équipements dans les environnements à risque explosif. Que faut-il en savoir ? Quelles conséquences sur les process et les équipements ? À quels coûts ? Voici les réponses aux questions fréquemment soulevées par les responsables de sites industriels.
En quoi l’industrie agroalimentaire est-elle concernée par l’ATEX ?
Qu’appelle-t-on une atmosphère explosive ATEX ?
Selon l’INERIS, expert public pour la maîtrise de risques industriels, une ATEX est « un mélange avec l'air, dans les conditions atmosphériques, de substances inflammables sous forme de gaz, vapeurs, brouillards ou poussières, dans lequel, après inflammation, la combustion se propage à l'ensemble du mélange non brûlé ».
En clair, une zone de production est catégorisée "ATEX" dès lors qu’il y a risque d’explosion. Ce risque explosif est notamment avéré si des équipements générant chaleur ou étincelles sont en contact avec des matières inflammables. Parmi ces matières inflammables, les carburants, combustibles ou gaz sont intuitivement identifiés. Il est cependant une autre source potentielle d’explosion : les poudres, les fines et les poussières en suspension dans l’air.
Sucre, farine, amidon, céréales, café, poudre de lait et tous les ingrédients secs en général constituent un danger d’inflammation ou d’explosion potentiel qu’il est nécessaire d’évaluer.
Quelles sont les normes européennes ATEX ?
Notons tout d’abord que le terme "normes" est ici erroné. Le risque explosif fait en réalité l’objet de deux directives européennes ATEX :
- Directive 1999/92/CE : pour les utilisateurs, les industriels qui utilisent les équipements.
- Directive 2014/34/UE : pour les constructeurs, les concepteurs fabricants des équipements.
Si une norme fixe concrètement les moyens applicables, une directive se contente d’imposer des résultats à atteindre. Laissant souvent place à interprétations. Il est fréquent d’assister à un dialogue de sourds entre un utilisateur pas toujours bien au fait de ses obligations et les constructeurs qui entretiennent parfois une certaine ambiguïté sur le niveau réel de protection des matériels.
Quelles sont les responsabilités de l’exploitant et du constructeur en matière d’ATEX ?
Dans un premier temps, il est nécessaire de fixer les responsabilités des uns et des autres :
- Il incombe aux industriels donneurs d’ordre de fournir l’étude de risques sous la forme du Document Relatif à la Protection Contre les Explosions.
- Il est de la responsabilité des constructeurs de concevoir l’installation qui répond au cahier des charges découlant de l’étude de risque.
Le responsable du site industriel fait l’inventaire des risques, met en place des mesures de prévention, délimite et caractérise les zones sensibles. C’est ce que l’on appelle le zonage ATEX.
Par exemple, une présence permanente de poussières dans l’environnement génère un classement en zone 20 (risque très élevé). Tandis qu’une présence de poussières rare génère un classement en zone 22 (risque faible).
Le fabricant de matériel ATEX, s’engage à concevoir et fabriquer des appareils qui répondent aux exigences en fonction du zonage ATEX. Il fournit une déclaration UE de conformité (zones 21 et 22) et une attestation d’examen UE de type par un organisme extérieur (zones 20).
Ce qu’il faut retenir :
- Il est de la responsabilité de l’exploitant de déterminer le matériel et les équipements de protection nécessaires pour assurer la sécurité des salariés dans les usines agroalimentaires.
- Il est de la responsabilité du fournisseur d’équipements de livrer les matériels conformes au cahier des charges et à la directive ATEX en particulier.
Tous les équipements de transfert de poudres doivent-ils être conformes ATEX ?
Selon le rapport 2019 du site dustsafetyscience.com, les poussières agroalimentaires sont à l’origine de plus de 40% des explosions industrielles. Pour autant, il ne s’agit pas de généraliser l’exigence ATEX la plus stricte à l’ensemble des équipements de manutention des poudres, ce qui génèrerait un surcoût d’installation et d’exploitation.
Comment éviter de surévaluer le risque ATEX pour le transfert et le dosage des poudres alimentaires ?
Les conséquences financières d’un zonage ATEX ne se limitent pas au surcoût à l’achat des machines compatibles avec une utilisation en atmosphère explosive. Des mesures de protection variées doivent être instaurées, des plans d’actions mis en place et le personnel formé régulièrement.
L’équation consiste à éviter des dépenses non indispensables dans une logique de rentabilité, sans jamais déroger à la protection des travailleurs, des biens et de l’environnement.
Bien menée, l’analyse des risques ATEX apporte plusieurs bénéfices :
- Éviter des zonages ATEX non nécessaires ;
- Caractériser correctement le niveau de risque (zone 20 – 21 ou 22).
Les experts APIA Technologie sensibilisent les industriels aux bonnes pratiques d’une démarche ATEX, sans se substituer à l’exploitant du site, seul responsable de l’évaluation des risques. De plus, un référent ATEX intervient pour les questionnements plus pointus qu’ils soient d’ordre sécuritaire, technique ou même juridique.
Quelles mesures de prévention peuvent éviter un classement en zone ATEX ?
Avant d’établir le zonage définitif d’un process industriel, il est recommandé de mettre en place toutes les mesures de prévention possibles pour diminuer les risques :
- En agissant sur les sources d’inflammation, comme une température ambiante trop élevée.
- En limitant la présence de matière inflammable dans l’atmosphère, comme les poussières en suspension dans l’air.
La gestion des flux d’ingrédients secs dans une usine agroalimentaire impacte ainsi directement le risque d’explosion. Un transport des poudres en milieu clos et la mise en place de système de dépoussiérage limitent en effet la production de fines. Et cela peut générer beaucoup d’économies !
Tous les équipements ATEX se valent-ils ?
3 catégories de certification ATEX pour répondre aux 3 catégories de risques
La directive ATEX constructeur prévoit trois catégories de matériels. À chaque catégorie correspond un niveau d’engagement du fabricant des équipements :
- Simple contrôle interne (cat. 3D pour zones ATEX22) ;
- Contrôle interne avec dépôt d’un dossier auprès d’un organisme notifié (cat. 2D pour zones ATEX 22/21) ;
- Attestation d’examen de type par un organisme extérieur avec audits annuels du Système d’Assurance Qualité (cat. 1D pour zones ATEX 22/21/20).
Chez APIA, nous sensibilisons nos clients industriels sur l’importance de s’intéresser de près aux certifications de leurs partenaires. Des équipements similaires peuvent en réalité présenter des différences de conception et de sécurité majeures mais peu visibles.
Un matériel de catégorie 2D ou 3D, auto-certifié, ne sera utilisable qu’en zone 22 ou 21. Pour être utilisable dans toutes les zones ATEX poussières, le matériel devra être certifié 1D par un organisme extérieur.
L’engagement norme ATEX agroalimentaire chez APIA Technologie
Dès 2005, APIA Technologie mène une réflexion profonde sur les réponses techniques dans le cadre ATEX. La démarche de certification de nos équipements de transfert par vis flexible est engagée à cette époque avec pour objectif de garantir le niveau de sécurité maximum. Aux tests internes, succèdent les validations et les audits confiés à l’INERIS.
En 2007, l’ensemble de nos matériels de transfert et de dosage de la gamme Transitube® obtiennent l’autorisation de mise sur le marché en catégorie 1. Depuis, le système d’assurance qualité en place dans nos ateliers permet de reconduire cette certification.
Mal comprises et mal appliquées, les directives ATEX sont souvent subies comme un cadre réglementaire de plus avec son lot de contraintes. Il ne faut pourtant jamais oublier qu’elles permettent de sauver des vies et des entreprises. Une mise en application cohérente et constructive de la réglementation ATEX au sein d’un site agro-alimentaire génère même des effets de bord extrêmement positifs : amélioration de la qualité et de l’hygiène, diminution de la pénibilité et réduction des coûts d’exploitation.
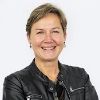
Juliette LARRODÉ
Responsable Marketing
Échangez avec un expert
Vous avez un projet d'optimisation de vos lignes industrielles ? Profitez de l'expérience des équipes APIA Technologie, spécialiste de l'agroalimentaire.
prendre rendez-vous