Reducing line stoppages, making for a productivity gain.
For its Charmes (88) factory, the PatisFrance-Puratos group was looking to automate the feeding of a roller grinder located downstream of a roasting kiln for dried fruit.
The raw materials are stored in cartons
Before going through the roasting kiln, the dried fruit is packaged in cartons weighing 5 to 10 kg.
Extraction under the roasting kiln from a mobile bag emptying station
At the outlet of the dried fruit roasting kiln, PatisFrance-Puratos installed a mobile feeder station in order to transfer the raw materials to a roller grinder. “This installation has allowed us to increase our productivity,” the Technical Manager explains. “Handling by operators and line stoppages are now very limited. We could have opted for installing a stationary Transitube® auger but the mobile feeder station offered greater flexibility. ”
Indeed, the Charmes factory has found two other uses for its new equipment. “We receive our dried fruit partially in cartons. Thanks to the mobile feeder station, the operator can easily prepare 500 kg big bags that will feed the roasting kiln. The ergonomics at this station have been improved substantially. ”
PatisFrance-Puratos has pushed even further the use of this innovation developed by the Apia Technologie teams. “The mobile feeder station proved to be ideal for transporting chocolate buttons to a praline mixer. In this process, we have removed the ergonomic strain linked to tasks that until now were performed manually. ”
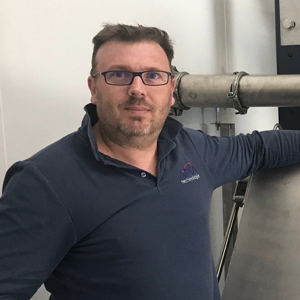
Hermann TESSIER
Sales engineer
Talk to an expert
Do you have a project to optimize your industrial lines? Take advantage of the experience of APIA Technologie teams specializing in the food industry.
REQUEST A CALLBACK