Filiale du groupe Lactalis, la société laitière de L’Hermitage (35) souhaitait augmenter ses capacités de production. Le spécialiste de la filière produits laitiers investit donc dans un second incorporateur.
Pour transférer les poudres vers cette nouvelle machine, l'industriel fait appel à APIA Technologie. L'objectif est d'adapter le circuit de transfert de poudre existant installé en 2005 et toujours en fonctionnement.
Les matières premières sont stockées en big-bag et en sacs
Les matières premières (poudres de lait, de cacao, d’amidon, sucre ou gélifiants) sont conditionnées en big-bag de 800 t ou en sacs de 25 kg. Deux stations de vidange big-bags sont en place, ainsi q'un vide-sacs pour les micro-ingrédients.
Un process repensé avec plus de flexibilité pour réduire les temps morts entre deux productions
« Nous cherchions à augmenter nos capacités de production, via l’ajout d’un second incorporateur de poudres, en nous appuyant sur le dispositif d’alimentation existant, précise le responsable process.»
Depuis 2005, la société laitière de l’Hermitage avait opté pour une ligne de transfert de poudre alimentée par deux vis flexibles, l’une dédiée aux produits dits noirs et l’autre dédiée aux matières premières dites blanches.
Au-delà de l'ajout d'un second incorporateur, le process d'alimentation a été plus largement repensé afin d'accélérer le retour sur investissement du nouvel équipement.
« Il était essentiel de limiter les temps morts entre les cycles de production. Désormais, une ligne d’alimentation est dédiée aux poudres de lait quand la seconde, via un bypass, est capable d’alterner entre les produits blancs et le cacao. »
Résultat : un gain de 30% de productivité.
Améliorer l'hygiène et la qualité
La société laitière de l’Hermitage a profité de la modernisation de son installation pour revoir l’implantation des deux vis flexibles en place et opter pour des tubes anti-abrasion en inox.
L'objectif était d'augmenter la résistance à l'abrasion pour plus de durabilité et de faciliter le démontage pour réduire le temps de nettoyage.
L'ensemble répondant aux contraintes ATEX.
« Les deux spires de 5 m chacune restent entièrement démontables ce qui assure un nettoyage optimal. Nous avons aussi conservé la possibilité de doser en ligne, de manière automatique, des micro-ingrédients, afin de réaliser des pré-mélanges à sec. »
Comme souvent, la problématique capacitaire a généré un cercle vertueux : qualité, hygiène, simplicité.
Grâce à la réflexion sur le transfert des ingrédients secs, c'est le process en général qui a été bonifié.
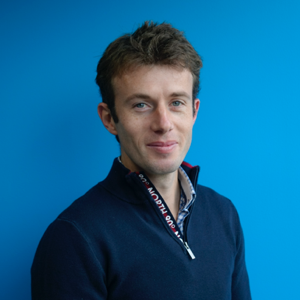
Alexandre TORCHARD
Ingénieur commercial
Échangez avec un expert
Vous avez un projet d'optimisation de vos lignes industrielles ? Profitez de l'expérience des équipes APIA Technologie spécialiste de l'agroalimentaire.
prendre rendez-vous